Our Commitment to Quality
Our commitment to quality has never changed.
We aim to create products that are truly customer-oriented.
We have successfully developed the VOLUTE™ Dewatering Press, something that has never been done before. Our strength lies in the fact that we have developed sludge dewatering presses and thickeners and have used them as a user. Because we have been using the dewatering press as a user as well, we can relate to our customers who are dealing with sludge daily on-site, thereby providing them with products that suit their needs.
We will continue to focus on quality from our customers’ perspective and engage in “monozukuri” (manufacturing) to deliver products that satisfy them.
Strict Quality Control Management
We strictly control quality by establishing a system by the ISO9001 certification regulations obtained in 2001.
Take, for example, ring-shaped parts that are used in all sludge dewatering presses in large numbers. At first glance, it may look easy to manufacture these parts, but because they are subject to burrs and distortions that cannot be removed by machine alone. Therefore, we inspect all parts and complete them by hand. We are very particular about manufacturing.
In the machine assembly process, we conduct a total of more than 300 inspections, including incoming inspections of procured parts, intermediate inspections in processes such as assembly, piping, and wiring, and comprehensive inspections after assembly. We ship products that have successfully passed all these inspections.
To make inspections more reliable, we review the methods and procedures periodically, and create inspection jigs, etc. to establish a reliable and detailed inspection system with no loose ends.
*The number of inspection items varies depending on the model.
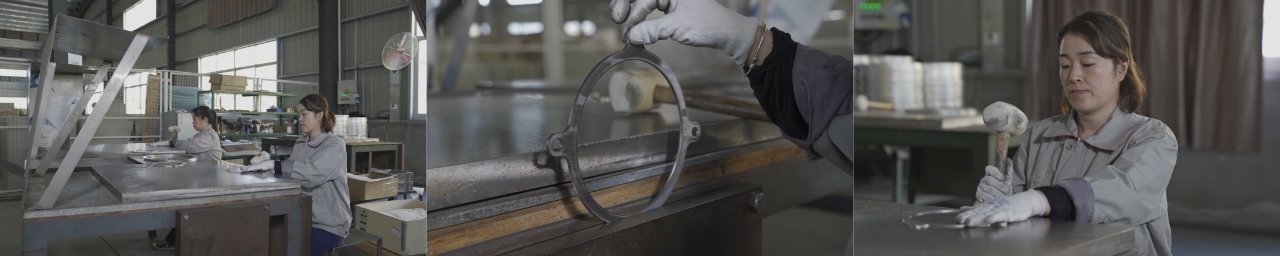
After-sales Service as a Part of Product Quality
Although our machines are designed with a focus on safety, performance, and maintainability so that customers can use them for as long as possible, they are not maintenance-free systems. Regular maintenance and parts replacement are essential.
In addition, because these machines treat wastewater or sludge, which are like living organisms with individual differences, no universal design can handle all substances. The machine requires operational settings adapted to the on-site conditions at the time, and in some cases, the machine may need to be customized after delivery. Our service does not end with the sale of the product. Our expert service engineers perform maintenance work, actually see and hear what is going on on-site, ponder on the best solution for the customer, and make proposals.
As a “user,” we have been involved in sludge treatment for decades and performed maintenance on-site with our customer. That’s what makes it possible for us to provide such after-sales service. We continue to commit the quality of our proposal capabilities.
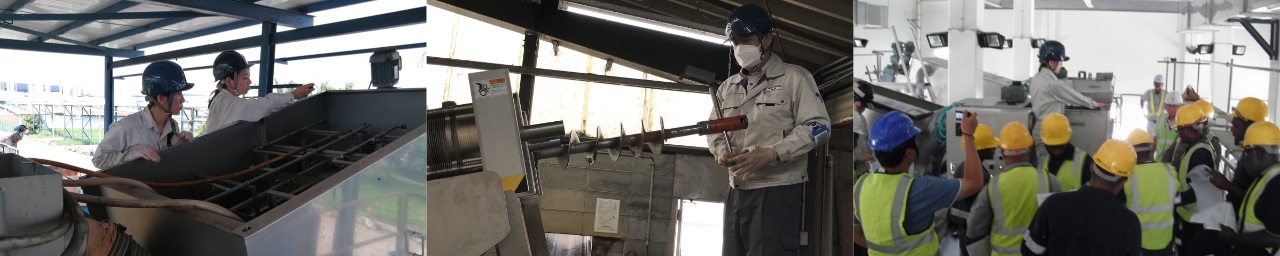
Commitment to Appearance
Although the machines are subject to contamination with sludge immediately after delivery, we pursue manufacturing that is aesthetically pleasing from the time of selection of parts procurement to the completion of the product.
Take, for example, stainless steel that is a key component of sludge dewatering presses and has excellent corrosion resistance. Since we are particular about the beauty of our products in an unpainted state, we strictly check for scratches or stains during acceptance inspection, and after completion, we polish them beautifully before delivering them to our customers.
Even if it is not directly related to the performance, we make no compromise on even the smallest details such as making sure the piping is processed level, plumb, or parallel to the frame of the machine with a lot of care and attention.
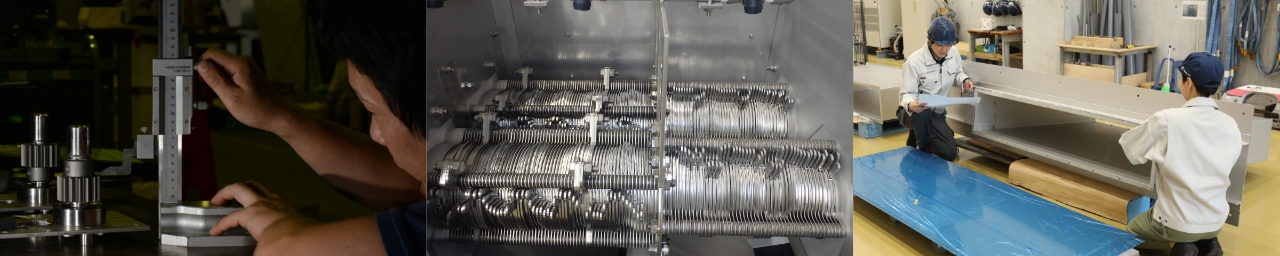